高雷雷 張金中 沙 磊
[1.中國(guó)石油大學(xué)(華東)機(jī)電工程學(xué)院;2.山東省無(wú)石棉摩擦材料技術(shù)研究推廣中心]
摘要采用Ansys軟件建立了等通道轉(zhuǎn)角擠壓的有限元模型,對(duì)不同模具角度條件下等通道轉(zhuǎn)角擠壓過(guò)程進(jìn)行了模擬,獲得了摩擦應(yīng)力、試樣與模具內(nèi)部應(yīng)力與應(yīng)變隨模具角度的變化。以AZ31鎂合金為試驗(yàn)對(duì)象,進(jìn)行了等通道轉(zhuǎn)角擠壓試驗(yàn),對(duì)模擬分析結(jié)果與試驗(yàn)結(jié)果進(jìn)行了對(duì)比。結(jié)果表明,等通道轉(zhuǎn)角擠壓過(guò)程中試樣與模具表面會(huì)產(chǎn)生較大摩擦應(yīng)力,導(dǎo)致試樣與模具內(nèi)應(yīng)力與應(yīng)變分布不均勻,摩擦應(yīng)力、材料內(nèi)部應(yīng)力及應(yīng)變隨著模具角度增加而減小。擠壓后AZ31鎂合金微觀組織被細(xì)化,理論分析結(jié)果與試驗(yàn)結(jié)果一致。
鎂合金具有密度低、比強(qiáng)度高、比彈性模量大、散熱性好、減震性好、承受沖擊載荷能力強(qiáng)等優(yōu)點(diǎn),近年來(lái)在汽車、電子器件及航空航天等行業(yè)得到了廣泛應(yīng)用。現(xiàn)在常用的鑄造鎂合金存在一定的鑄造缺陷,限制了其應(yīng)用范圍。因此,采用塑性成形工藝制備高性能鎂合金成為研究熱點(diǎn)。
等通道轉(zhuǎn)角擠壓(Equal Channel Angular Extru-sion,簡(jiǎn)稱ECAE)與其他塑性變形工藝相比,可以通過(guò)純剪切變形來(lái)細(xì)化材料的微觀組織,具有擠壓前后不改變?cè)嚇有螤、擠壓過(guò)程可以多次重復(fù)進(jìn)行、顯著細(xì)化組織等一系列獨(dú)特的優(yōu)點(diǎn),成為一種具有廣闊應(yīng)用前景的強(qiáng)烈塑性變形方法。ECAE制備超細(xì)晶材料,逐漸受到研究者的普遍關(guān)注并進(jìn)行了大量的研究。雖然ECAE工藝已被證明在獲得超細(xì)晶與高性能合金材料方面具備一定優(yōu)勢(shì),但目前該工藝還沒(méi)有規(guī)模工業(yè)化應(yīng)用。一般采用加熱進(jìn)行多次試驗(yàn)的方法進(jìn)行擠壓,效率較低,且試驗(yàn)過(guò)程中經(jīng)常出現(xiàn)由于摩擦應(yīng)力過(guò)大導(dǎo)致的斷裂及裂紋等現(xiàn)象,造成擠壓失敗。雖然有研究者采用有限元分析對(duì)ECAE進(jìn)行了數(shù)值模擬,但對(duì)ECAE過(guò)程中摩擦應(yīng)力隨模具角度的變化還未見(jiàn)報(bào)道。因此,分析ECAE擠壓過(guò)程中摩擦應(yīng)力對(duì)擠壓的影響,研究試樣在擠壓過(guò)程中的應(yīng)力及塑性應(yīng)變的大小分布,對(duì)快速制定不同材料的ECAE工藝,加速該工藝的實(shí)際應(yīng)用具有積極意義。
本課題建立了多種有限元模型,對(duì)不同條件下的ECAE進(jìn)行了有限元模擬,分析了模具角度變化對(duì)摩擦應(yīng)力、試樣變形及塑性應(yīng)變等大小及分布的影響,并對(duì)AZ31鎂合金進(jìn)行了ECAE擠壓試驗(yàn),將試驗(yàn)結(jié)果與理論分析進(jìn)行了對(duì)比驗(yàn)證,獲得了摩擦應(yīng)力、塑性應(yīng)變、試樣與模具內(nèi)應(yīng)力等隨模具內(nèi)角的變化規(guī)律。
1有限元分析模型建立及試驗(yàn)方法
1.1有限元模型建立
采用有限元分析軟件Ansys建立等通道轉(zhuǎn)角擠壓的分析模型,試樣及模具選用plane182單元,試樣與模具接觸面采用接觸對(duì)單元target169與contact171單元。實(shí)際擠壓時(shí)試樣與模具表面潤(rùn)滑良好時(shí)摩擦因數(shù)一般在在0.1以下,故有限元模擬時(shí)試樣與模具表面摩擦因數(shù) μ設(shè)定為0.1。模具內(nèi)角p變化范圍為110°~130°,模擬時(shí)試樣尺寸為100 mm×10 mm。通道內(nèi)角p為120°時(shí)等通道轉(zhuǎn)角擠壓劃分網(wǎng)格后的有限元分析模型見(jiàn)圖1。
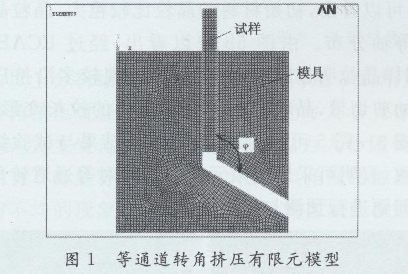
1.2試驗(yàn)材料
試驗(yàn)材料為AZ31鎂合金棒材,其化學(xué)成分見(jiàn)表1。從棒材上切割的試樣尺寸為10 mm ×10 mm×100mm,與有限元模擬尺寸一致。對(duì)試樣進(jìn)行表面處理后表面粗糙度Ra=0.8~3.2μm,擠壓時(shí)表面涂覆潤(rùn)滑劑,試樣與模具表面間摩擦因數(shù)約為0.1。
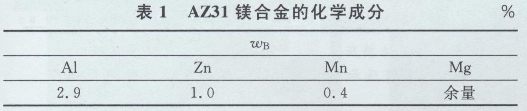
1.3試驗(yàn)方法
ECAE采用了不同通道內(nèi)角的模具進(jìn)行了擠壓試驗(yàn),模具通道橫戳面尺寸均為10 mm ×10 mm。擠壓時(shí)加熱溫度為300℃,加熱時(shí)間為30 min。試樣與模具達(dá)到加熱溫度與保溫時(shí)間后,在液壓萬(wàn)能試驗(yàn)機(jī)上對(duì)試樣進(jìn)行擠壓。
2 結(jié)果分析與討論
2.1 摩擦應(yīng)力變化
模具內(nèi)角p分別為110 °、120°與130°條件下試樣與模具接觸面間的摩擦應(yīng)力大小及分布見(jiàn)圖2。由圖2a可以看出,在p為110°時(shí),無(wú)論是在豎直通道還是在斜通道,試樣與模具接觸表面均存在較大的摩擦應(yīng)力,豎直通道內(nèi)最大摩擦應(yīng)力值約為47 MPa,轉(zhuǎn)角處最大摩擦應(yīng)力值約為149 MPa。由圖2b可以看出,在p為120°時(shí),在豎直通道內(nèi)試樣與模具接觸表面摩擦應(yīng)力與110°時(shí)相比分布區(qū)域顯著減少,摩擦應(yīng)力大小也顯著降低。豎直通道內(nèi)最大摩擦應(yīng)力值減小為23 MPa,轉(zhuǎn)角處最大摩擦應(yīng)力值約為118 MPa。由圖2c可以看出,在p為130°時(shí),在豎直通道內(nèi)試樣與模具接觸表面僅存在部分區(qū)域產(chǎn)生了摩擦應(yīng)力,且摩擦應(yīng)力進(jìn)一步降低,豎直通道內(nèi)最大摩擦應(yīng)力值減小為13.8 MPa,轉(zhuǎn)角處最大摩擦應(yīng)力值為159 MPa。由圖2還可以看出,3種模具內(nèi)角條件下,在模具轉(zhuǎn)角處均發(fā)生摩擦應(yīng)力集中現(xiàn)象。該處摩擦應(yīng)力值顯著大于其余區(qū)域摩擦應(yīng)力值,且試樣兩側(cè)摩擦應(yīng)力方向相反。
有限元分析結(jié)果表明,模具內(nèi)角p對(duì)摩擦應(yīng)力的分布及摩擦應(yīng)力的大小均有影響。在等通道轉(zhuǎn)角擠壓過(guò)程中,試樣與模具接觸表面會(huì)產(chǎn)生較大的摩擦應(yīng)力。隨著模具角度增加,豎直通道內(nèi)摩擦應(yīng)力分布區(qū)域面及應(yīng)力值均減小,最大摩擦應(yīng)力值出現(xiàn)在轉(zhuǎn)角處。由等通道轉(zhuǎn)角擠壓可知,當(dāng)試樣在轉(zhuǎn)角處發(fā)生剪切變形時(shí),試樣除了發(fā)生剪切塑性變形外,轉(zhuǎn)角處試樣內(nèi)部產(chǎn)生一個(gè)較大的變形抗力,試樣具有一個(gè)被壓縮變粗的趨勢(shì),因此會(huì)產(chǎn)生一個(gè)由內(nèi)至外的脹力。在試樣下行過(guò)程中,在此脹力作用下試樣表面與模具表面產(chǎn)生較大的摩擦應(yīng)力。而試樣在等通道轉(zhuǎn)角擠壓過(guò)程中,模具內(nèi)角的改變會(huì)影響試樣與模具接觸間隙及所需擠壓力大小的改變。擠壓力與接觸面積的變化導(dǎo)致摩擦應(yīng)力隨著模具角度的改變而發(fā)生變化。試樣在發(fā)生剪切變形時(shí),在剪切變形作用下由矩形變?yōu)槠叫兴倪呅,因而試樣上下表面塑性變形時(shí)流變速度不一致,試樣下表面與上表面反向移動(dòng),導(dǎo)致試樣兩表面摩擦應(yīng)力方向不一致。

為了驗(yàn)證摩擦應(yīng)力對(duì)擠壓的影響,采用內(nèi)角p=110 °與120°模具在摩擦因數(shù)為0.1條件下對(duì)AZ31鎂合金進(jìn)行了等通道轉(zhuǎn)角擠壓試驗(yàn)。擠壓后試樣表面外觀形貌見(jiàn)圖3。由圖3a可以看出,p=110°條件下試樣上表面出現(xiàn)裂紋,p=120°時(shí)試樣表面無(wú)裂紋產(chǎn)生。
試驗(yàn)采用A231鎂合金的屈服強(qiáng)度為140 MPa,而由圖2可知,p =110 °時(shí)擠壓過(guò)程中轉(zhuǎn)角處的最大摩擦應(yīng)力為149 MPa,p=120°擠壓過(guò)程中轉(zhuǎn)角處的最大摩擦應(yīng)力為118 MPa。p=110°最大摩擦應(yīng)力值大于AZ31鎂合金的屈服強(qiáng)度,而p=120°最大摩擦應(yīng)力值小于AZ31鎂合金的屈服強(qiáng)度,故p=110°時(shí)試樣出現(xiàn)裂紋而p=120°時(shí)無(wú)裂紋出現(xiàn)。由模擬結(jié)果可知,p=110°時(shí)除轉(zhuǎn)角處外其余區(qū)域摩擦應(yīng)力值均小于鎂合金屈服強(qiáng)度,故裂紋僅在試樣上表面產(chǎn)生。試驗(yàn)結(jié)果與模擬結(jié)果一致。
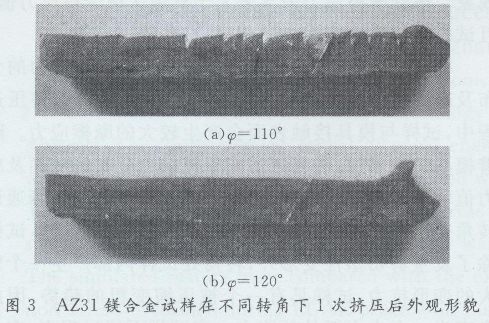
2.2試樣變形情況
圖4為有限元模擬的試樣在ECAE擠壓過(guò)程中的變形情況?梢钥闯,試樣在經(jīng)過(guò)轉(zhuǎn)角處后發(fā)生明顯的剪切變形,劃分的有限元網(wǎng)格沿剪切方向被拉長(zhǎng)。試樣前端存在翹曲現(xiàn)象,試樣最下端由初始的直線變?yōu)閺澢螤睿岸嗣嫘纬梢欢ɑ《,?jīng)過(guò)轉(zhuǎn)角后試樣下端的上表面與模具之間出現(xiàn)一個(gè)小的間隙。由圖3還可以看出,試樣經(jīng)過(guò)轉(zhuǎn)角處后,試樣內(nèi)部變形不均勻,試樣前端雖發(fā)生翹曲且形狀變化較大,但試樣前端內(nèi)部網(wǎng)格被拉長(zhǎng)的剪切變形量卻較小,網(wǎng)格無(wú)明顯變化。斜通道內(nèi)轉(zhuǎn)角處至試樣前端翹曲段之間區(qū)域內(nèi)部網(wǎng)格被剪切拉長(zhǎng)變形現(xiàn)象較明顯,且變形量基本一致。
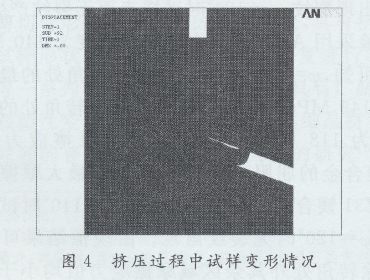
對(duì)比圖3與圖4可以看出,經(jīng)ECAE處理后試樣的外觀形狀與模擬結(jié)果一致,試樣前端出現(xiàn)翹曲現(xiàn)象,且試樣下表面出現(xiàn)彎曲現(xiàn)象。圖5為未經(jīng)ECAE擠壓處理與經(jīng)不同道次擠壓處理后A231的微觀組織。由圖5a可以看出,初始材料的晶粒比較粗大,晶粒晶界明顯呈等軸分布。由圖5b可以看出,經(jīng)過(guò)ECAE處理后,試樣晶粒明顯細(xì)化,微觀組織出現(xiàn)較多沿?cái)D壓方向分布的剪切帶,晶粒出現(xiàn)沿剪切方向的拉長(zhǎng)變形現(xiàn)象。結(jié)合圖3~圖5可以得出,理論分析結(jié)果與試驗(yàn)結(jié)果基本一致,表明可采用有限元模擬方法對(duì)等通道轉(zhuǎn)角擠壓中的問(wèn)題進(jìn)行預(yù)測(cè)與驗(yàn)證。
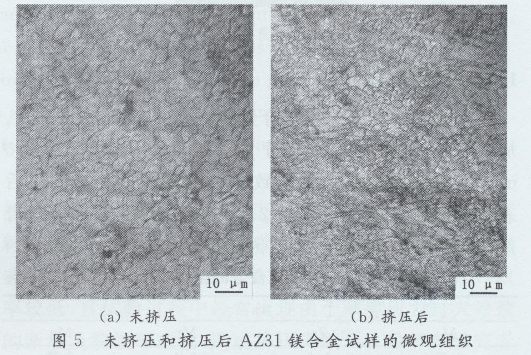
2.3應(yīng)力變化
模具內(nèi)角p分別為110 °、120°與130°條件下試樣與模具應(yīng)力分析見(jiàn)圖6。由圖6a可以看出,在110°時(shí),試樣內(nèi)部應(yīng)力分布較均勻,應(yīng)力大小基本一致,試樣內(nèi)部應(yīng)力大小約為600 MPa。模具內(nèi)不同區(qū)域其應(yīng)力大小不同,模具最大應(yīng)力出現(xiàn)在模具斜通道試樣下表面與模具接觸的A區(qū)域,該區(qū)域應(yīng)力大小約為600 MPa。外模具豎直通道與試樣頂端接觸區(qū)域及斜通道兩側(cè)B區(qū)域也存在較大應(yīng)力,應(yīng)力大小約為400 MPa,其余C區(qū)域應(yīng)力大小約為200 MPa。由圖6b可以看出,在120°時(shí),試樣內(nèi)部應(yīng)力分布不均勻,應(yīng)力分布主要由兩部分組成:在轉(zhuǎn)角處及斜通道試樣與模具接觸的下表面區(qū)域應(yīng)力大小約為648 MPa,其余區(qū)域應(yīng)力大小約為518MPa。擠壓過(guò)程中在模具內(nèi)部產(chǎn)生較大應(yīng)力的區(qū)域面積與110°模具相比有所減小,主要集中在斜通道兩側(cè)。轉(zhuǎn)角處試樣下表面與模具接觸的Al區(qū)域應(yīng)力值約為389 MPa,Bl與Cl區(qū)域應(yīng)力大小分別約為259 MPa和130 MPa。由圖6c可以看出,在130°時(shí),試樣內(nèi)部應(yīng)力分布也不均勻,應(yīng)力分布與120°模具類似,主要由兩部分應(yīng)力組成,在轉(zhuǎn)角處及斜通道試樣與模具接觸的下表面區(qū)域應(yīng)力大小約為600 MPa,其余部分區(qū)域應(yīng)力大小約為400 MPa。在模具內(nèi)部產(chǎn)生較大應(yīng)力的區(qū)域面積進(jìn)一步減小,在轉(zhuǎn)角處及試樣最下端與模具接觸A2區(qū)域應(yīng)力大小約為400 MPa,B2區(qū)域應(yīng)力大小約為200MPa。
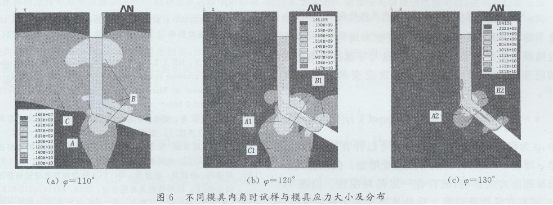
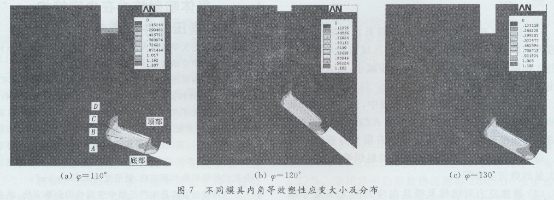
由以上分析結(jié)果可知,隨著模具內(nèi)角p的增加,等通道轉(zhuǎn)角擠壓過(guò)程中試樣及模具內(nèi)應(yīng)力大小及存在區(qū)域面積均發(fā)生變化。試樣及模具內(nèi)應(yīng)力大小隨模具角度增加有下降趨勢(shì),試樣內(nèi)應(yīng)力隨模具角度增加出現(xiàn)應(yīng)力分布不均的現(xiàn)象,而模具內(nèi)應(yīng)力影響區(qū)域面積隨著模具角度增加顯著減小。由摩擦應(yīng)力模擬結(jié)果可知,在等通道轉(zhuǎn)角擠壓過(guò)程中,試樣表面與模具表面之間會(huì)產(chǎn)生較大的摩擦應(yīng)力,且試樣與模具內(nèi)應(yīng)力分布及大小變化趨勢(shì)與摩擦應(yīng)力隨模具角度的變化趨勢(shì)相一致,這說(shuō)明摩擦應(yīng)力影響了試樣及模具內(nèi)的應(yīng)力分布,導(dǎo)致模具角度較小時(shí)模具內(nèi)應(yīng)力較大。而隨著模具角度增加,摩擦應(yīng)力分布區(qū)域與應(yīng)力值減小,使模具與試樣內(nèi)應(yīng)力分布與應(yīng)力值相應(yīng)減小。
2.4塑性應(yīng)變變化
等通道轉(zhuǎn)角擠壓時(shí),試樣在經(jīng)過(guò)轉(zhuǎn)角后發(fā)生剪切塑性變形,而模具為彈性變形,無(wú)塑性變形產(chǎn)生。模具內(nèi)角分別為110 °、120°與130°條件下試樣等效塑性應(yīng)變變化情況見(jiàn)圖7。為了便于說(shuō)明,將斜通道內(nèi)試樣的等效塑性應(yīng)變由底部到頂部分4個(gè)區(qū)域。4個(gè)區(qū)域分別為:試樣底部的A區(qū)域,靠近試樣底部的B區(qū)域,靠近試樣頂部的C區(qū)域和試樣頂部的D區(qū)域。由圖7可以看出,在3種模具角度情況下,應(yīng)變分布規(guī)律類似,試樣內(nèi)部塑性應(yīng)變?cè)诓煌瑓^(qū)域大小不同。試樣應(yīng)變大小由A到D區(qū)域逐步增大,靠近試樣頂部的D區(qū)域等效應(yīng)變最大。由圖7還可以看出,在模具內(nèi)角p=110°時(shí)豎直通道內(nèi)試樣上端有塑性應(yīng)變產(chǎn)生,但在其余模具角度該部位無(wú)塑性應(yīng)變產(chǎn)生。4個(gè)區(qū)域等效塑性應(yīng)變隨模具內(nèi)角的變化見(jiàn)圖8。由圖8可以看出,隨著模具內(nèi)角p增加,試樣內(nèi)部等效塑性應(yīng)變逐步減小。
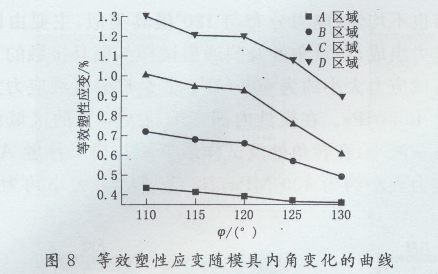
當(dāng)試樣與模具表面處于理想狀態(tài)無(wú)摩擦應(yīng)力時(shí),試樣內(nèi)部應(yīng)變不均勻是由于試樣在經(jīng)過(guò)轉(zhuǎn)角發(fā)生剪切變形時(shí),試樣上下表面塑性流動(dòng)速度不一致,試樣內(nèi)部變形量不均勻,導(dǎo)致試樣內(nèi)部等效應(yīng)變不均勻。等效應(yīng)變隨模具角度增加而逐漸減小,這與等通道轉(zhuǎn)角擠壓剪切應(yīng)變的計(jì)算結(jié)果相一致,等效應(yīng)變的計(jì)算公式為:

式中, Ψ為模具外角角度。由上式可以計(jì)算出,當(dāng)模具內(nèi)角p增加時(shí),試樣內(nèi)部的等效應(yīng)變?cè)黾。但該公式未考慮摩擦應(yīng)力的影響,故存在一定的局限性。由圖7a可知,試樣在豎直通道最上端處雖還未發(fā)生剪切變形,但該處仍存在較大應(yīng)變,這是因?yàn)楫?dāng)模具內(nèi)角較小時(shí),豎直通道內(nèi)也分布有較大的摩擦應(yīng)力。試樣在向下移動(dòng)過(guò)程中,在摩擦應(yīng)力作用下導(dǎo)致試樣在豎直通道內(nèi)產(chǎn)生一定的塑性應(yīng)變。而實(shí)際進(jìn)行擠壓時(shí),由于摩擦應(yīng)力的存在,導(dǎo)致試樣表面在進(jìn)行等通道轉(zhuǎn)角擠壓時(shí),試樣與模具接觸表面在摩擦力作用下產(chǎn)生粘滯效應(yīng),阻礙了試樣表面的金屬流動(dòng),加劇了試樣表面等效應(yīng)變與試樣心部應(yīng)變量的不均勻程度。因此,實(shí)際進(jìn)行等通道轉(zhuǎn)角擠壓時(shí),應(yīng)采用較小摩擦因數(shù)的試樣和模具,以保證晶粒細(xì)化效果的均勻性。
3 結(jié) 論
(1) ECAE擠壓過(guò)程中試樣與模具接觸表面會(huì)產(chǎn)生較大的摩擦應(yīng)力,摩擦應(yīng)力的分布區(qū)域面積與摩擦應(yīng)力的大小隨著模具角度的增加而逐步減小,最大摩擦應(yīng)力出現(xiàn)在轉(zhuǎn)角處。
(2)試樣在等通道轉(zhuǎn)角擠壓過(guò)程中,試樣前端發(fā)生翹曲,內(nèi)部網(wǎng)格剪切變形不均勻,對(duì)AZ31鎂合金進(jìn)行等通道轉(zhuǎn)角擠壓試驗(yàn)后試樣變形與有限元分析結(jié)果一致。通過(guò)微觀組織分析可觀察到晶粒組織被細(xì)化,且存在大量的剪切變形帶。
(3)摩擦應(yīng)力對(duì)試樣及模具內(nèi)應(yīng)力的大小及分布產(chǎn)生影響,模具內(nèi)角越小,模具內(nèi)應(yīng)力分布區(qū)域與應(yīng)力值越大,試樣內(nèi)塑性應(yīng)變大小隨模具內(nèi)角增加而減小,塑性應(yīng)變由于摩擦應(yīng)力影響而在試樣內(nèi)部分布不均勻。